Tajniki piaskowania
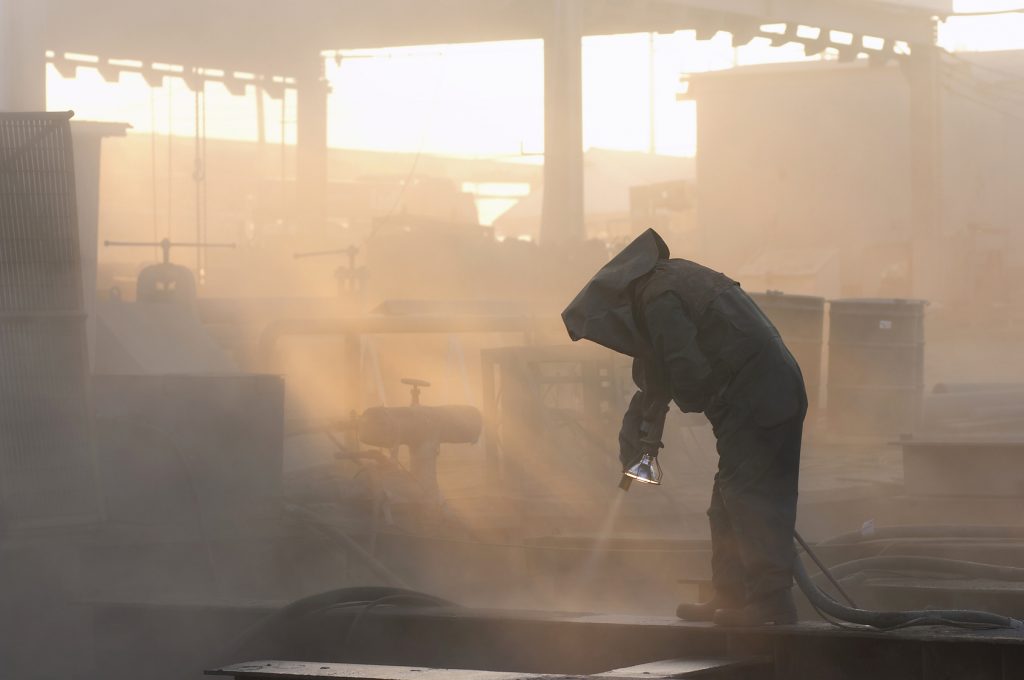
Technikę piaskowania opracował amerykański żołnierz i wynalazca Benjamin Chew Tilghman ponad 140 lat temu. Legenda głosi, że pomysł użycia piasku do obróbki różnych materiałów powstał, kiedy Tilghman obserwował na pustyni smagane piaskiem okna. Proces piaskowania opatentował najpierw w USA a później w Wielkiej Brytanii. Współcześnie jest to bardzo popularna technika matowienia oraz zdobienia szkła oraz innych materiałów, takich jak ceramika, kamień, tworzywa sztuczne, metale i drewno. Do procesu używane są piaskarki, które znaleźć można w różnych rodzajach, oferujących odmienne funkcje i komfort pracy. Istnieją dwa typy piaskowania: pyłowe i bezpyłowe. Do piaskowania pyłowego wykorzystuje się pistolety inżektorowe bądź ciśnieniowe. Są one podłączone do zasobnika, w którym znajduje się piasek kwarcowy. Piaskowaniem bezpyłowym nazywany jest proces, odbywający się w piaskarkach kabinowych, które posiadają zamknięty obieg ścierniwa.
Piaskarki ręczne, półautomatyczne i automatyczne
Piaskarki dzielą się na piaskarki ręczne, półautomatyczne i automatyczne. W ręcznych piaskarkach kainowych cały proces obróbki szkła wykonywany jest przez operatora. Można w nich obrabiać szkło o wysokości 100-120 cm. Urządzenia półautomatyczne wykorzystywane są przede wszystkim do obróbki całych powierzchni szkła. W większości z nich możliwe jest matowienie elementów o wysokości powyżej 160 cm. Proces piaskowania odbywa się ręcznie, natomiast tafla przesuwana jest automatycznie. Najbardziej zaawansowane są piaskarki automatyczne. Po załadowaniu tafli szkła na pas transportujący operator jedynie programuje na paneli dotykowym zakres pracy.
Ścierniwa wykorzystywane w piaskowaniu
W piaskowaniu używa się kilku rodzajów ścierniw. Najbardziej popularnym i najpowszechniej używanym jest piasek kwarcowy. Oczywiście musi być on starannie przesiany z zanieczyszczeń. Piasek jest ścierniwem ogromnie skutecznym. Z jego pomocą można wyczyścić konstrukcje stalowe, beton czy felgi i karoserię. Wykorzystuje się go także do renowacji obiektów mostowych, czyszczenia cegieł i starych obiektów oraz do hydropiaskowania. W zależności od rodzaju elementów do czyszczenia oraz przepustowości dyszy dobiera się odpowiednią granulację. 0,1 – 0,5 mm do czyszczenia zabytków oraz drobnych elementów, 0,3-1mm do piaskowania felg, karoserii, hydropiaskowania oraz oczyszczania i matowienia elementów metalowych. 0,8 – 1,4 mm lub 1,0 – 3,0 mm zalecany jest przy czyszczeniu konstrukcji stalowych o wysokim stopniu skorodowania lub piaskowania betonu.